The equipment inspection log filling in process is simple. Our editor enables you to work with any PDF form.
Step 1: On this website page, choose the orange "Get form now" button.
Step 2: After you have entered the editing page equipment inspection log, you'll be able to discover all of the options available for the document within the upper menu.
Feel free to type in the following details to create the equipment inspection log PDF:
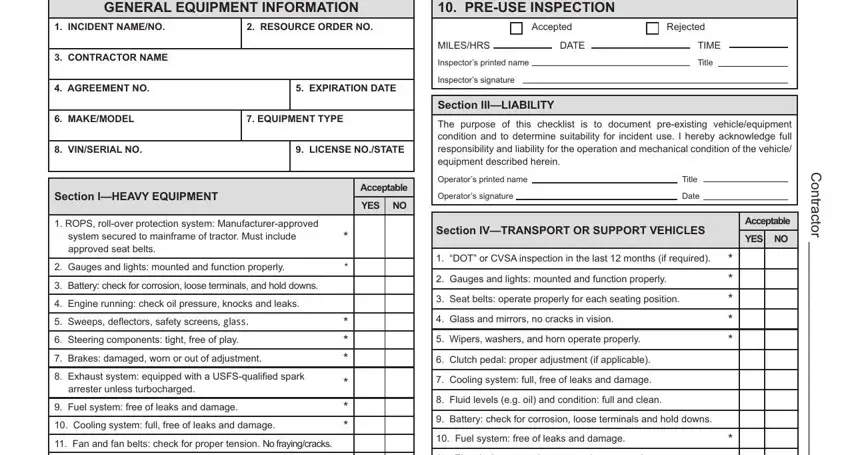
You should enter the data within the box Engine support equalizer bar, shackle bolts shifted spring leaf, Belly plate radiator guards, debris, Final drive transmission and, Sprocket and idlers crack in, no welds, Tracks and rollers no broken pads, Dozer and assembly trunnion bolts, Rear hitch drawbar serviceable, Body and cab condition describe, Equipment cleanliness all areas, All hydraulic attachments operate, cylinders hold at extension hose, and Backup or travel alarm minimum.
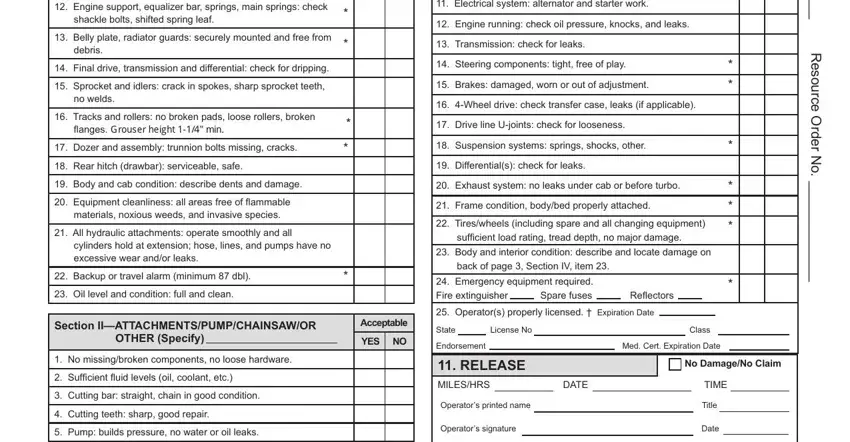
Note all particulars you may need within the section Engine starts idles and shuts off, Inspectors printed name, Title, Section VREMARKS, Describe all unsatisfactory items, Safety ItemDo not accept until, SEE SUPPLEMENTAL INFORMATION ON, PREVIOUS EDITION NOT USABLE, Printed on recycled paper, FINANCE COPY PREUSE, and OPTIONAL FORM REV.

Indicate the rights and responsibilities of the sides in the part GENERAL EQUIPMENT INFORMATION, PREUSE INSPECTION, INCIDENT NAMENO, RESOURCE ORDER NO, Accepted, Rejected, CONTRACTOR NAME, AGREEMENT NO, EXPIRATION DATE, MAKEMODEL, EQUIPMENT TYPE, VINSERIAL NO, LICENSE NOSTATE, MILESHRS, and DATE.
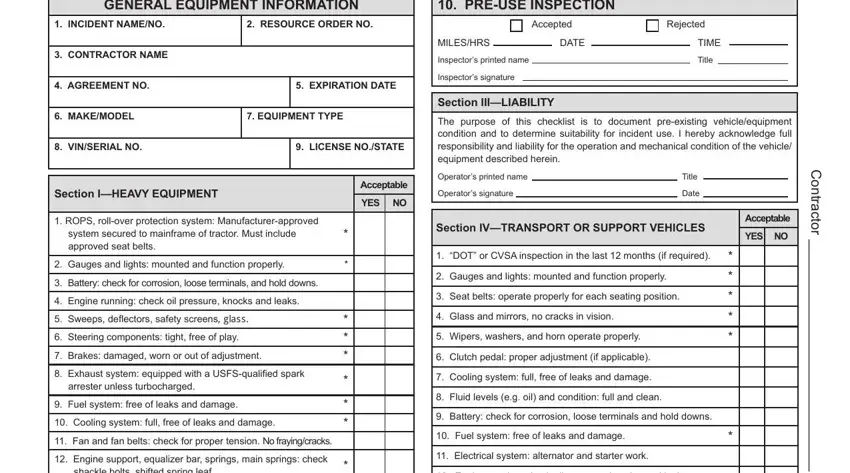
Finalize by taking a look at the next sections and filling them out as needed: shackle bolts shifted spring leaf, Belly plate radiator guards, debris, Final drive transmission and, Sprocket and idlers crack in, no welds, Tracks and rollers no broken pads, Dozer and assembly trunnion bolts, Rear hitch drawbar serviceable, Body and cab condition describe, Equipment cleanliness all areas, All hydraulic attachments operate, cylinders hold at extension hose, Backup or travel alarm minimum, and Oil level and condition full and.
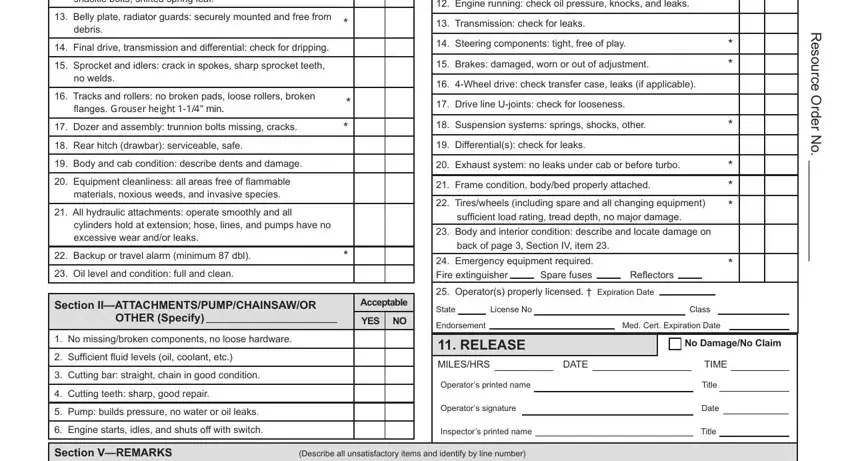
Step 3: Select the button "Done". Your PDF form may be transferred. You can upload it to your device or send it by email.
Step 4: Prepare a duplicate of each document. It should save you some time and make it easier to refrain from misunderstandings in the future. Keep in mind, your data isn't going to be used or analyzed by us.